Compresseur/générateur d'air à gaz de 16 pi3/min à 175 psi avec moteur Honda GX390
Compresseur/générateur d'air à gaz de 16 pi3/min à 175 psi avec moteur Honda GX390
Impossible de charger la disponibilité du service de retrait
Specifications
ENGINE
Honda GX390
CC
389
PSI
16 CFM @ 175 PSI
ENGINE START
Recoil & Electric
RUNNING WATTS
3500
MAX WATTS
4000
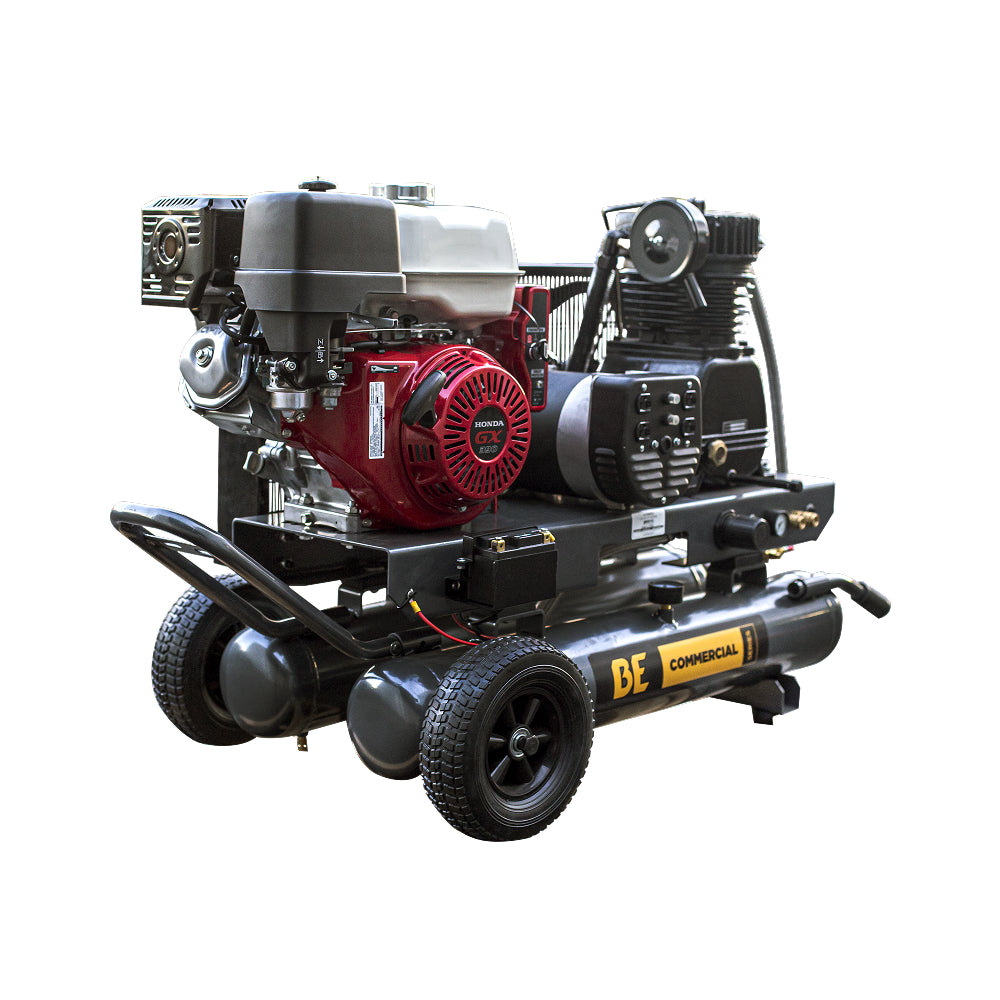
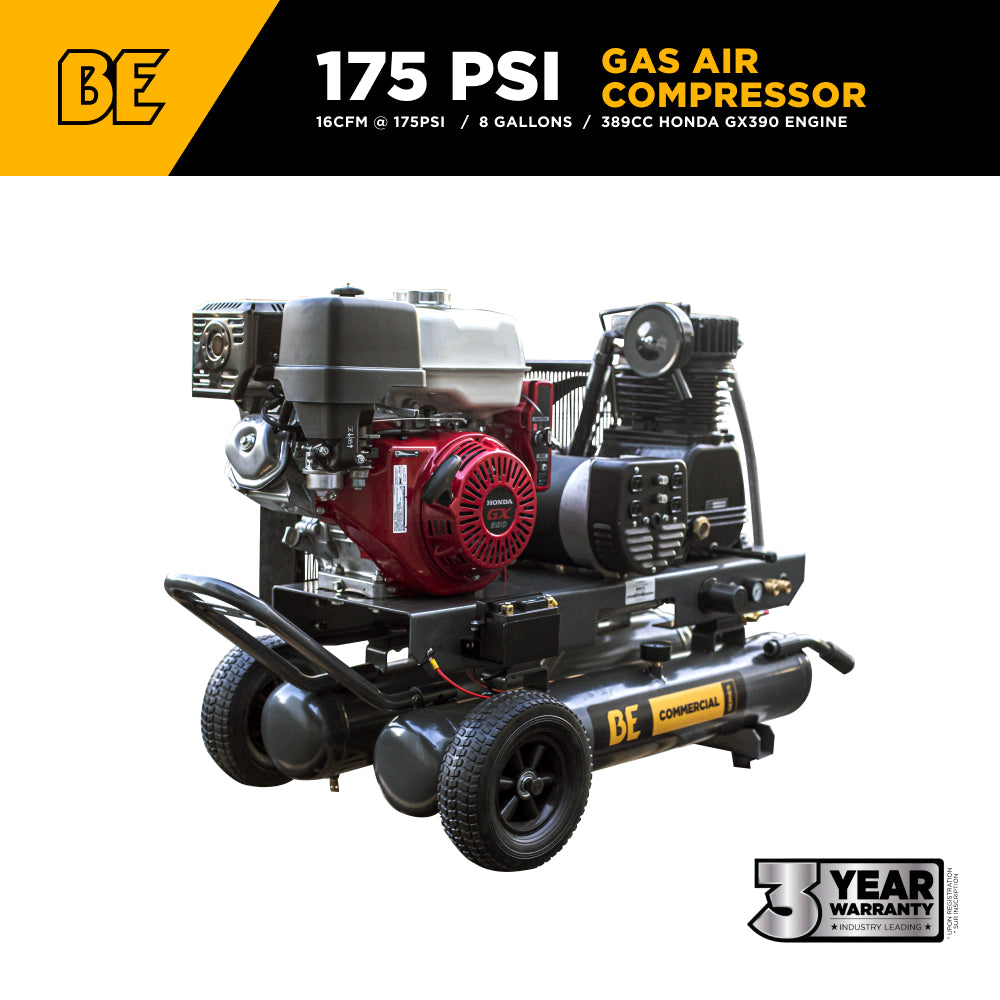
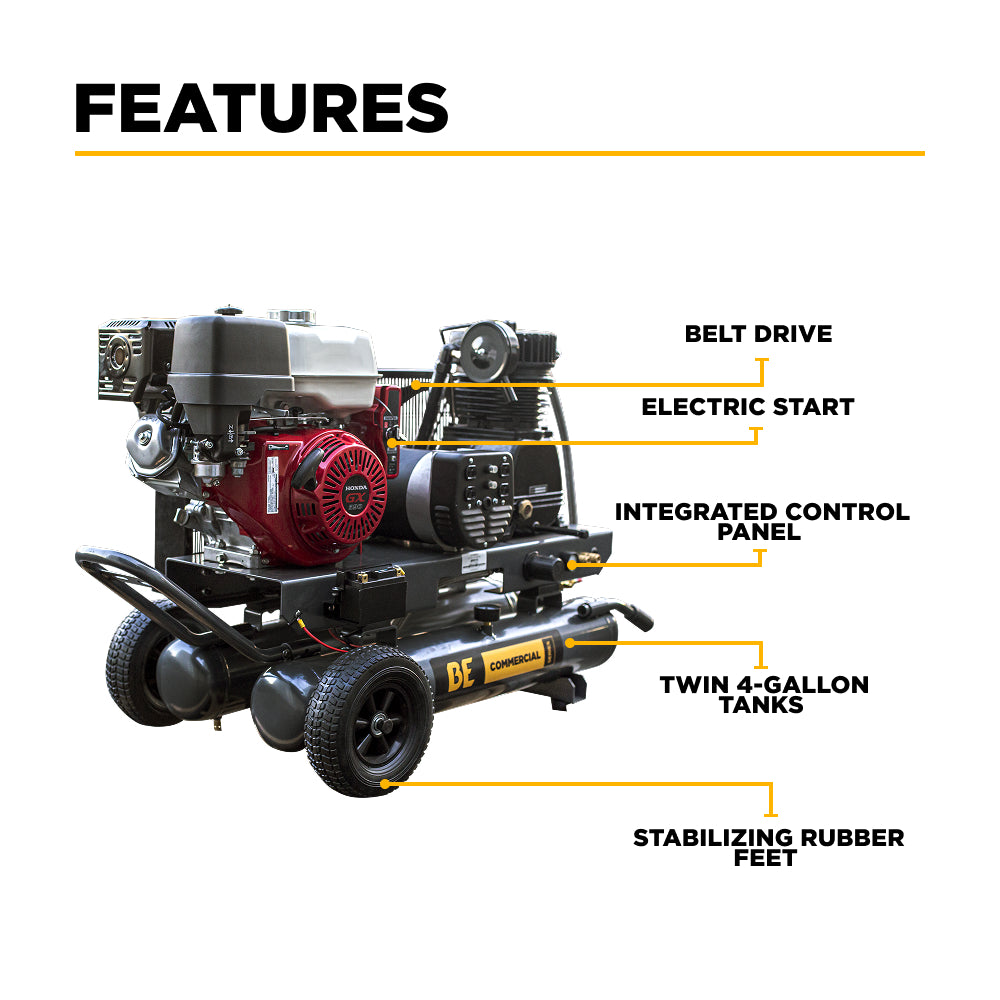
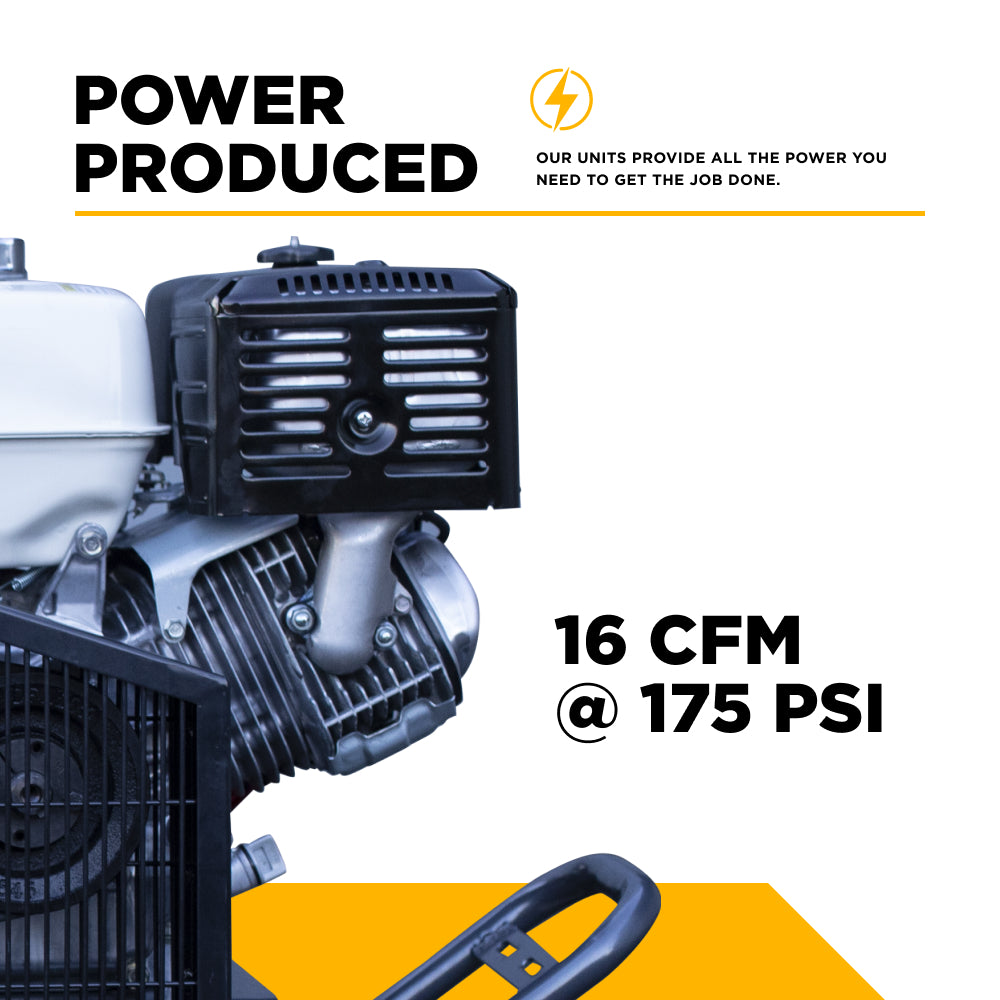
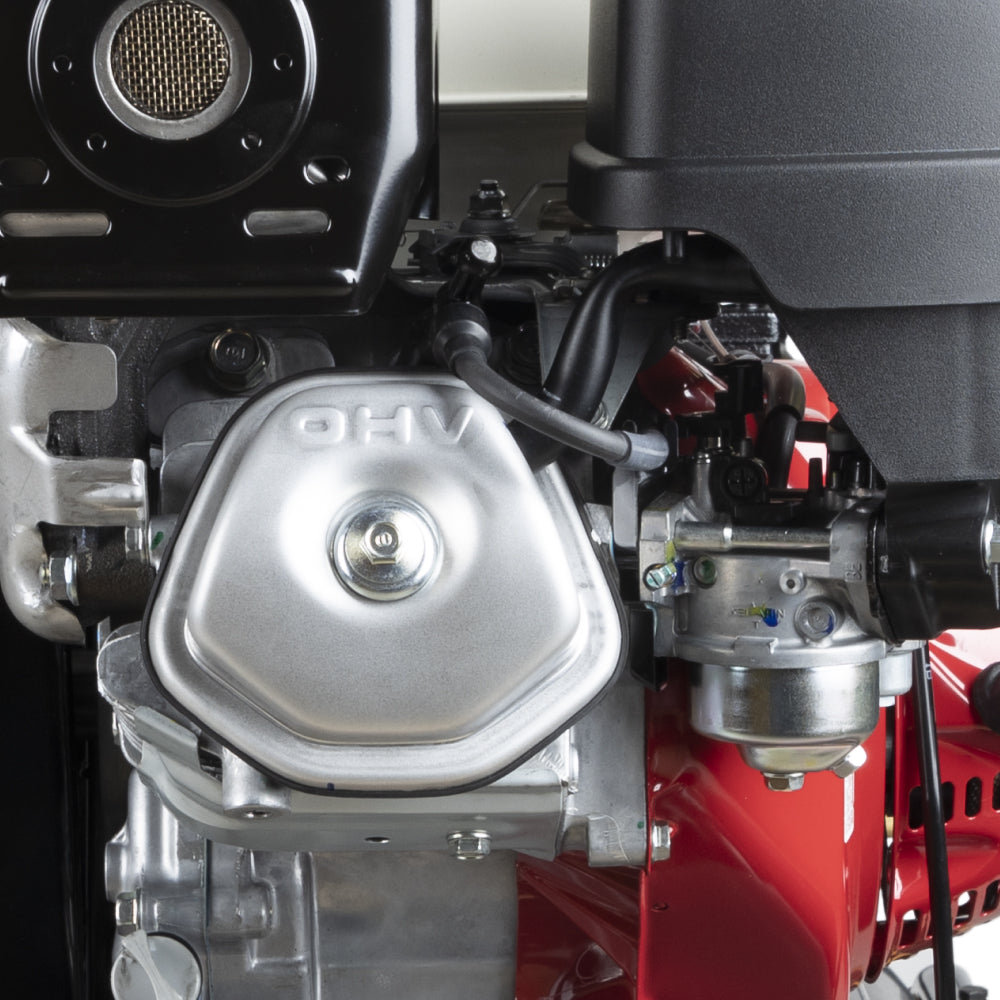
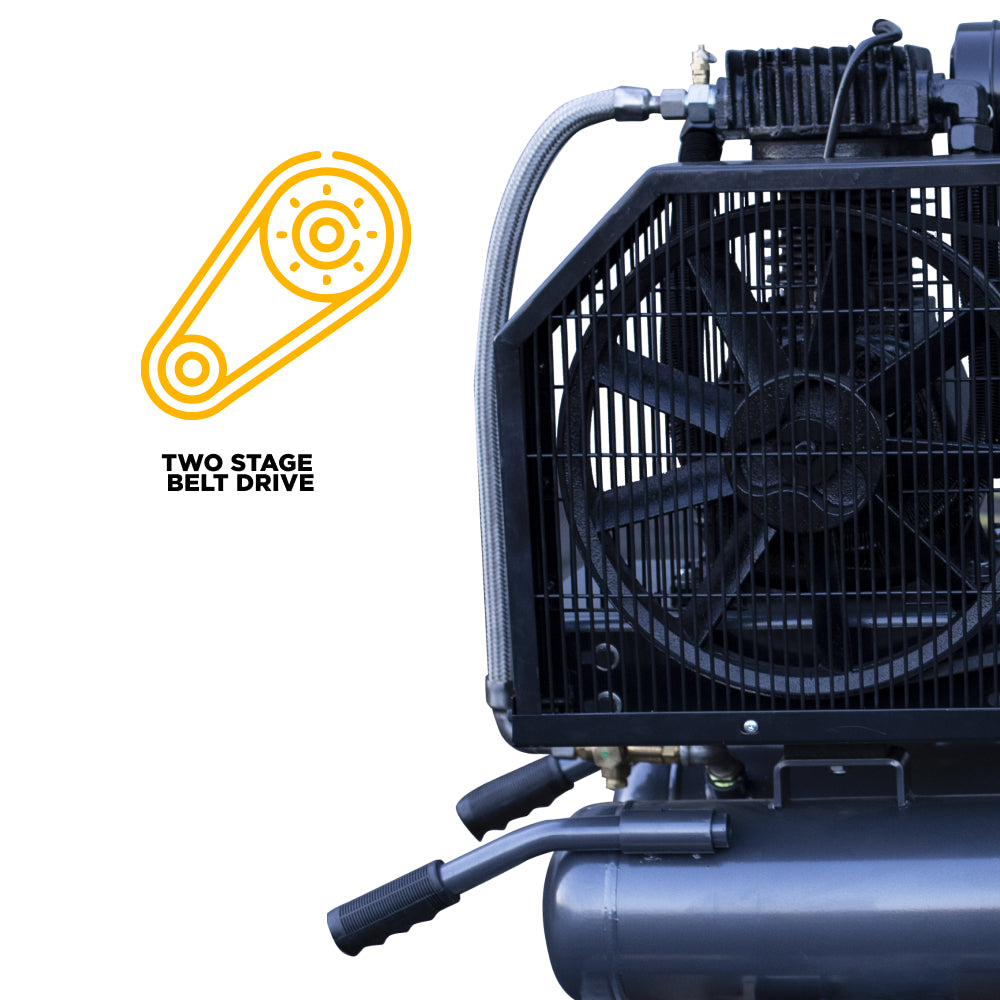
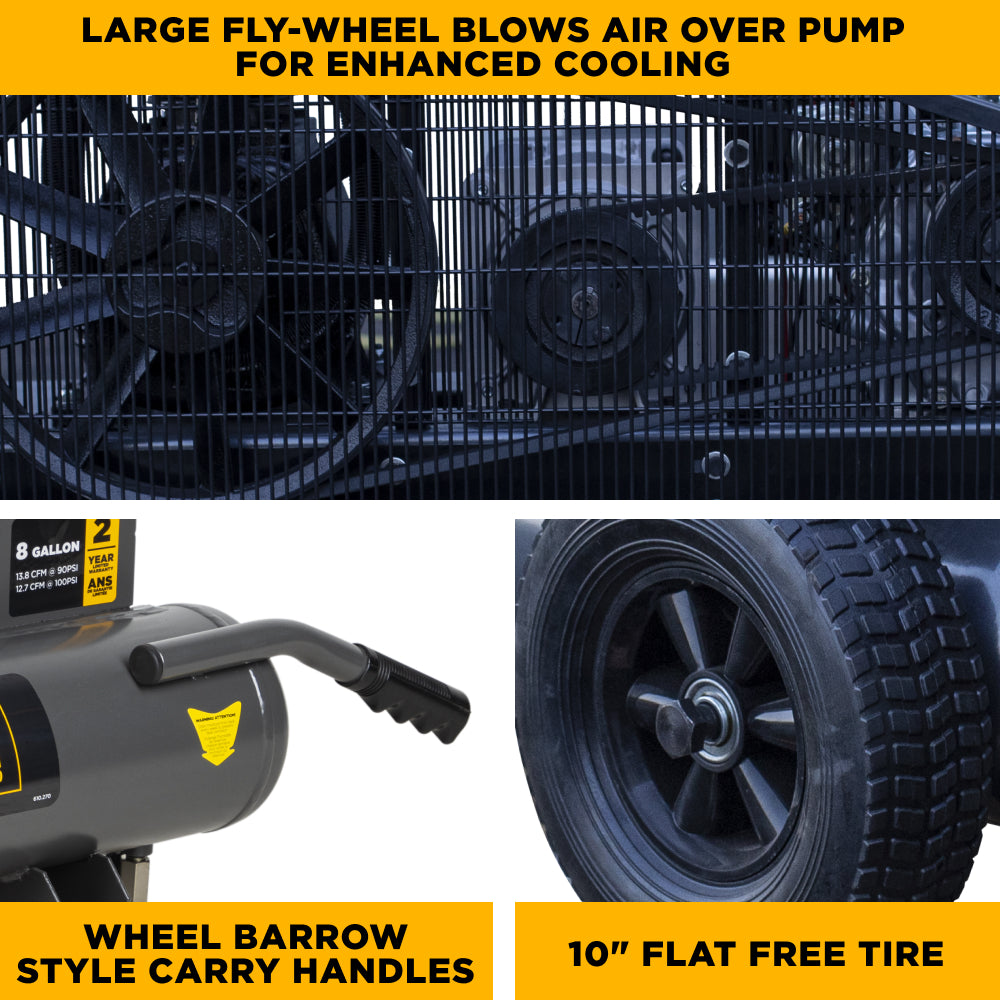
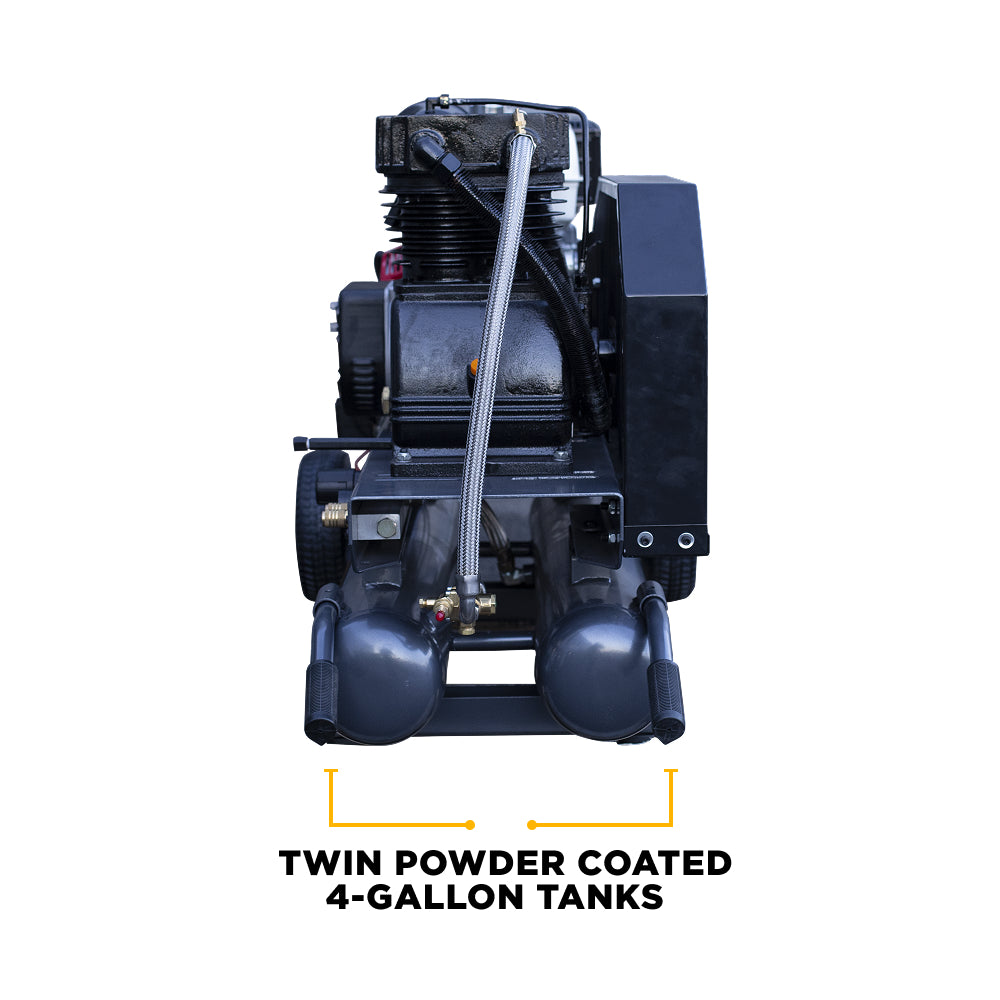
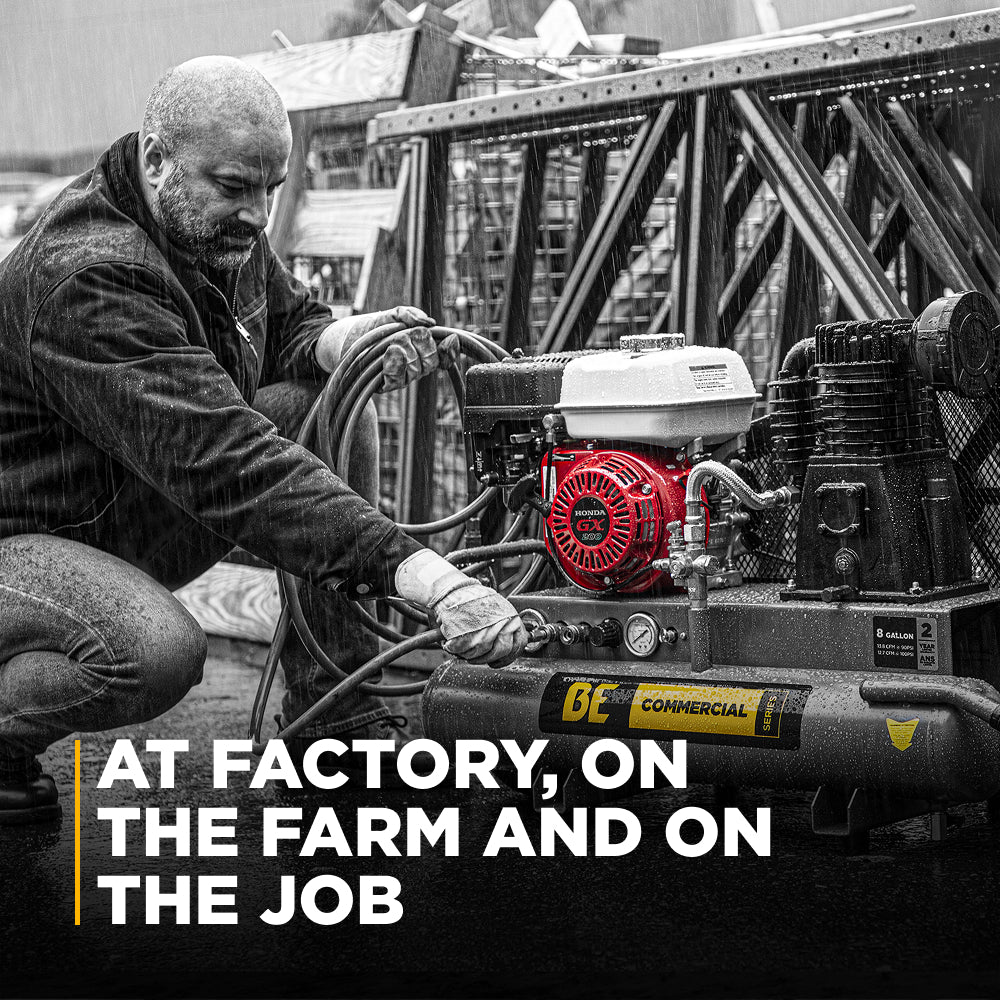
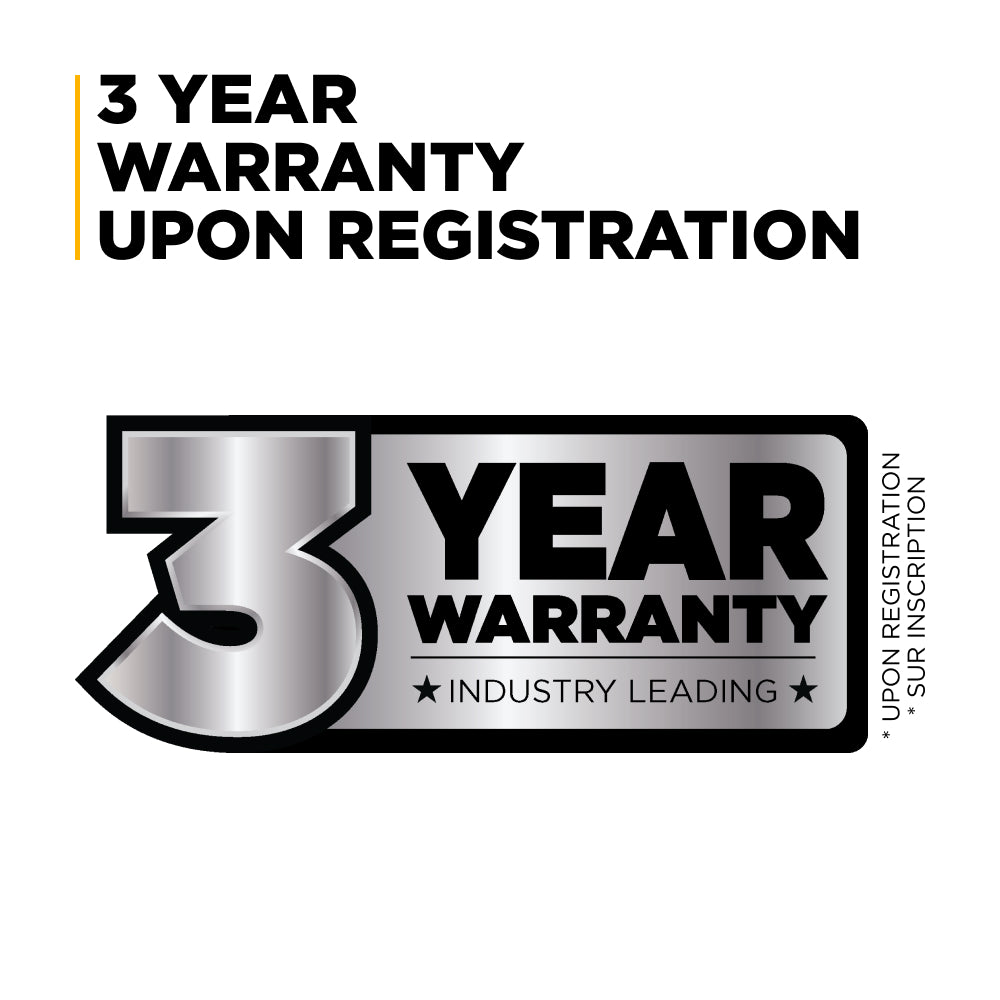
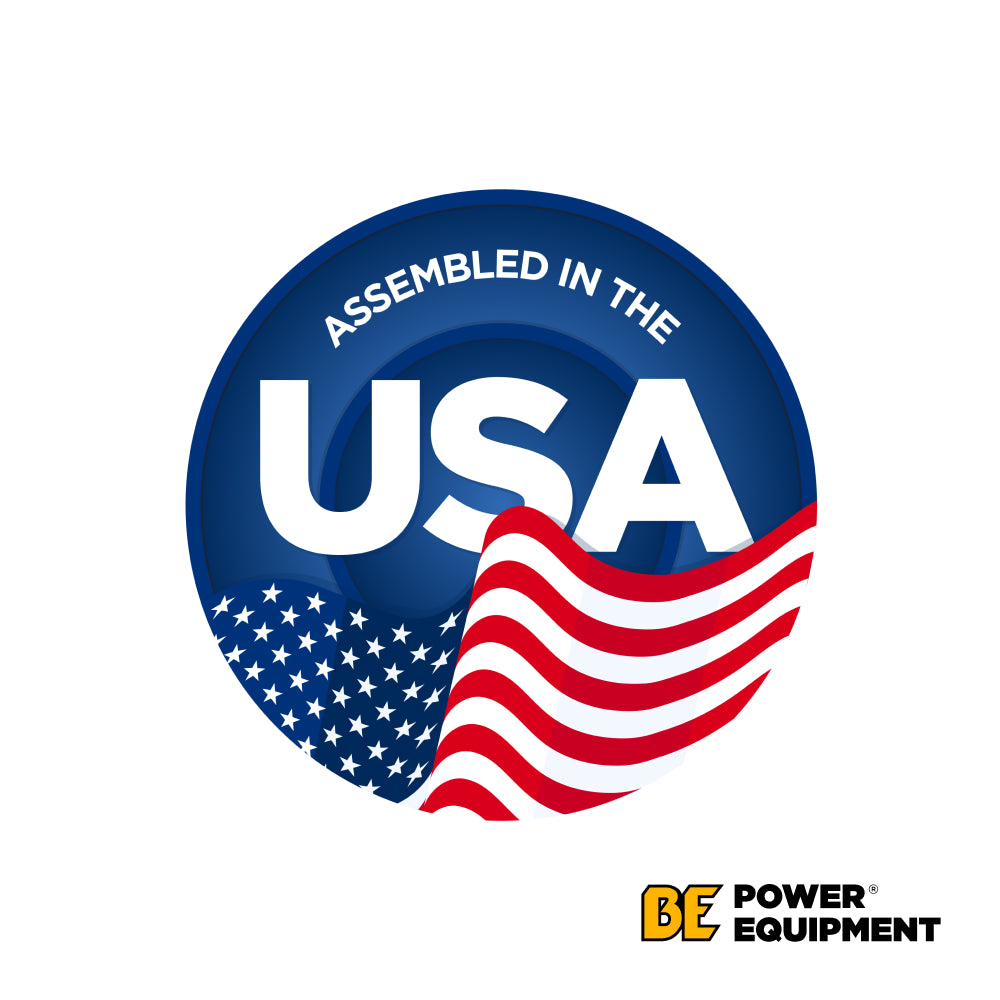
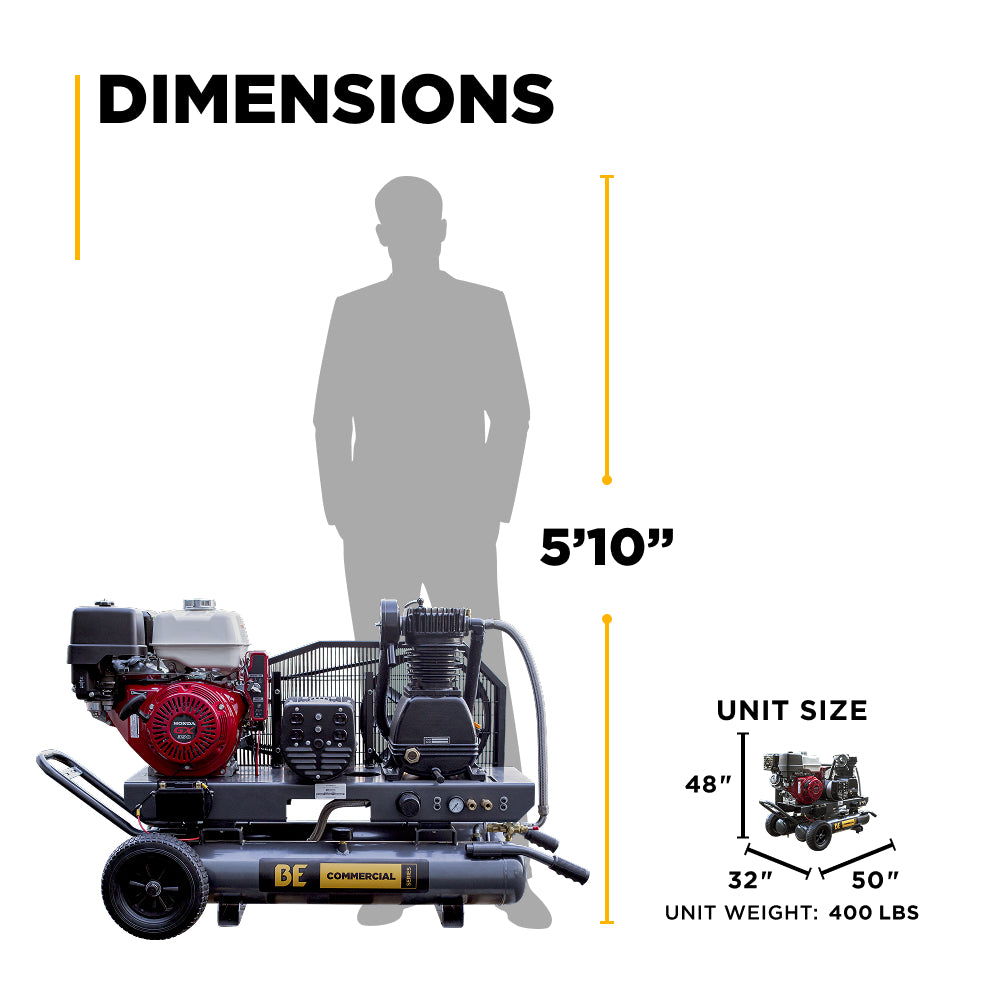
Product
Description
Moteur Honda de qualité commerciale avec un excellent rapport poids/puissance conçu pour être utilisé toute la journée, tous les jours.
Système de démarrage électrique avec batterie incluse.
Transmission par courroie Le système maintient le régime de la pompe bas et fonctionne à une température plus froide pour prolonger ses performances et sa durée de vie.
Pompe robuste à deux étages lubrifiée par barbotage avec des cylindres en fonte, des soupapes accessibles et des roulements aux deux extrémités du vilebrequin pour maximiser la longévité.
Vanne de décharge pilote est un Conrader américain réglé pour couper à 140 PSI et couper à 175 PSI.
Le générateur est alimenté par le moteur Honda et peut être utilisé en même temps que le compresseur.
Réservoirs jumeaux de 4 gallons sont revêtus de poudre pour une durabilité accrue et chacun dispose d'un orifice de vidange du réservoir à clapet à bille. Trous pré-percés dans les supports de stabilisation pour le montage dans un camion ou une remorque.
Selle amovible permettant à l'utilisateur de séparer le moteur/la pompe du réservoir pour des configurations spécialisées.
Le produit réel peut différer des images présentées sur le site Web.
INFORMATIONS SUR L'EXPÉDITION
POIDS : 550 LBS
DIMENSIONS (L x l x H) : 50"x32"x48"
Compare Air Compressor

Frequently Asked Questions about Air Compressor
What size portable air compressor do I need?
It all depends on what you’re using it for. If you’re just inflating car tires, sports equipment or using a small nail gun, a compact portable air compressor with a small tank (under 6 gallons) and low on CFM will be enough, and most of the time. Most of the text will be in the 15-20 word range.
But if you’re running tools that require continuous air, like impact wrenches, spray guns, grinders or sanders, you’ll need a bigger tank (20+ gallons) and higher CFM. This ensures the compressor can keep up with the air supply and without causing pressure drops or forcing the motor to overheat.
Also consider the maximum PSI your tools need. Most air tools run at 90 PSI but some may need more. Choosing a compressor that’s above your tool’s minimum PSI and CFM requirements by a little bit ensures smooth operation without constantly stressing the machine.
What are the types of air compressors?
Compressed air systems are everywhere, from construction and automotive to industrial applications. These systems use air compressors to generate the compressed air to power pneumatic tools, inflate car tires and do many other tasks. Portable air compressors are favorite for their ease of use, versatility and portability. When selecting a compressed air system it’s important to consider pressure, flow rate and power source to make sure the system meets your needs. Whether you’re on a construction site or in your home garage the right air compressor can make all the difference.
When it comes to choosing an air compressor understanding the different types is key. Gas powered compressors are good for remote locations or where there’s no electricity. They’re rugged and reliable, perfect for construction, landscaping and irrigation projects. Electric compressors are good for indoor use because they’re quiet and no exhaust fumes. Diesel powered compressors are another option, used in heavy duty industrial applications. Each type has its own advantages so consider your needs and the environment you’ll be working in when making your selection.
What is CFM, and why is it important?
CFM, or Cubic Feet per Minute, measures how much air volume the compressor can deliver at a certain pressure. It’s important because air tools and applications have specific CFM requirements to work properly. If your compressor doesn’t produce enough CFM your tools will run poorly or not at all.
Higher CFM ratings means the compressor can power more demanding tools or even multiple tools at once, that’s why understanding CFM is key. For example a framing nailer might only require 2-3 CFM but a pneumatic grinder might require 8-10 CFM. If you’re going to use tools back to back or run multiple air tools you’ll need a compressor with higher CFM rating.
Remember CFM is often rated at a specific PSI (usually 90 PSI). Always check the CFM at operating pressure not just the maximum pressure output to match it to your tool requirements.
What’s the difference between PSI and CFM?
PSI (Pounds per Square Inch) measures the pressure of the air, CFM measures the volume of air flow. Both are important but serve different roles in making sure your tools work properly. High PSI is about pressure force; CFM is about keeping that pressure going for longer periods.
For example a compressor might be able to generate high PSI but not deliver enough airflow (CFM) to run a high demand tool for very long. Conversely if the CFM is high but PSI is too low the tool might not operate at full power. Ideally a good air compressor balances both values.
When shopping for a compressor you should match both the CFM and PSI ratings to your tool needs as different products have different specifications. If your tool requires 90 PSI and 5 CFM but your compressor only delivers 3 CFM at 90 PSI you will run into performance issues.
Should I choose an oil-free or oil-lubricated air compressor?
Oil-free compressors are more convenient for many users because they require very little maintenance. They are lighter, cleaner and good for occasional or light use, like home DIY projects or inflating tires. Modern oil-free compressors use special coatings on their pistons to reduce wear without the need for lubrication.But oil-lubricated compressors are built for heavy use. They require adding and changing oil periodically but can handle heavy duty tasks for much longer without wearing out. These are more suited for contractors, auto shops and industries where compressors run for hours a day. Oil-lubricated compressors also come with replaceable filters to ensure clean air intake and prolong the compressor’s life.
If low noise, portability and less maintenance is what you’re looking for then an oil-free might be the way to go. If you’re planning long work sessions with demanding air tools then an oil-lubricated will serve you better in the long run.
How much maintenance does an air compressor need?
The level of maintenance your air compressor needs depends on whether it’s oil-free or oil-lubricated. Oil-lubricated compressors require you to check oil levels regularly and perform oil changes according to the manufacturer’s schedule. Using the correct type of oil is crucial to ensure long engine life and efficient performance.
In addition to oil care you should also check and clean or replace the air intake filter regularly. A dirty filter can cause your compressor to overheat or reduce efficiency. Drain the tank after every use to remove accumulated moisture which can cause rust and shorten the compressor’s life.
Inspect all hoses, fittings and seals periodically to catch leaks early. Tighten loose connections and replace any worn parts promptly. Following a regular maintenance schedule will ensure your compressor will operate reliably for years.
What are portable air considerations?
What type of pneumatic tools can I use?
Can I use an air compressor indoors?
How long can an air compressor run continuously?
INFORMATION
- The Company
- Customer Service
- Product Information
- Product Registration
- Technical Support
- About
- Warranty
- Terms and Conditions
- Privacy Policy
- Translation missing: en.general.social.links.linkedin
- YouTube
CONTACT DETAILS
30585A Progressive Way
Abbotsford, BC V2T 6W3
Telephone: +1 800-663-8331
Contact Us
ENGLISH CATALOGCatalogue FrancaisCatalogo Espanol
© 2024 Be Power Equipment
What are portable air considerations?
Portable air compressors offer many benefits including ease of use, portability and versatility. When selecting a portable air compressor consider factors such as weight, size and noise level. Look for models with sturdy wheels or handles for easy transport and a compact design for storage. Also think about the power source—gas or electric—and the pressure and flow rate requirements for your specific application. By evaluating these factors you can find the perfect portable air compressor that meets your needs whether you’re inflating tires, powering pneumatic tools or doing DIY projects around the house.
What type of pneumatic tools can I use?
Pneumatic tools such as impact wrenches, drills and sanders rely on compressed air to operate efficiently. These tools are used in various industries including construction, automotive and manufacturing due to their power and reliability. When selecting pneumatic tools consider factors such as power, speed and durability. Choose tools with high quality components, ergonomic design and minimal maintenance requirements for long lasting performance. By choosing the right pneumatic tools and pairing them with the right air compressor you can increase your productivity and make your work easier and more efficient.
Can I use an air compressor indoors?
Yes, but with some precautions. Electric air compressors are safe for indoor use because they don’t produce harmful exhaust fumes. They’re a great option for garages, workshops and basements where ventilation might be limited. Just ensure good airflow to prevent overheating especially if you’re working in a small enclosed space.
Gas-powered compressors on the other hand are not safe to use indoors because they emit carbon monoxide — an odorless deadly gas. These compressors must be operated outdoors or in very well-ventilated industrial environments.
Noise is another consideration. Some compressors even electric ones can be loud. Look for quieter models or enclosures if indoor noise is a concern especially if you’re working from home or in a residential neighborhood.
How long can an air compressor run continuously?
This depends on the compressor’s duty cycle — the manufacturer-specified ratio of time it can run compared to time it must rest. For example, a 50% duty cycle means it should run for 5 minutes and then cool off for 5 minutes. Exceeding the duty cycle can cause overheating and shorten compressor life.
Heavy-duty compressors designed for industrial or commercial use often have much higher duty cycles (sometimes up to 100%) making them a different kind of compressor compared to consumer-grade models. Consumer-grade or portable compressors usually have lower duty cycles and are intended for intermittent use.
Always check your specific model’s duty cycle and don’t push it beyond its limit. Allowing proper cooldowns and monitoring heat will extend the life of the compressor significantly.